Crush blades, integral components in various industrial applications, play a pivotal role in reducing large materials into smaller, more manageable pieces. These blades are used across a multitude of sectors, including waste management, recycling, manufacturing, and agriculture, to ensure efficient material processing. As industries continue to evolve, the design, efficiency, and functionality of crush blades are expected to undergo significant advancements. In this article, we will explore the future of crush blades, examining emerging trends, technological innovations, and their growing importance in modern industrial applications.
The future of crush blades is largely shaped by advancements in materials science, machine automation, and the increasing demand for efficiency and sustainability in industrial operations. To stay competitive, industries are continuously seeking solutions that reduce energy consumption, minimize maintenance costs, and extend the lifespan of their machinery.
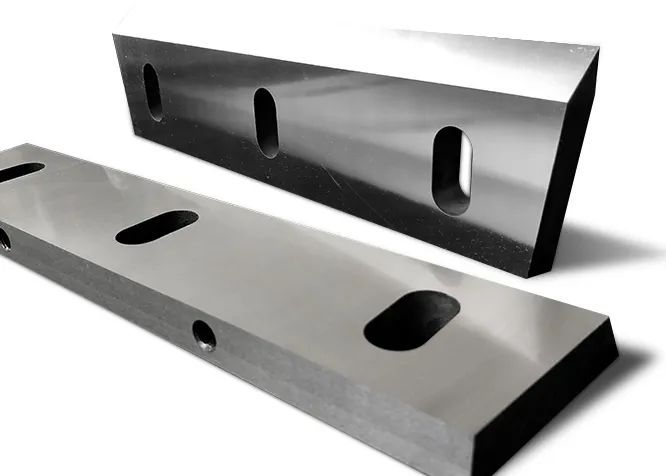
The Growing Demand for Crush Blades
As industries evolve and face new challenges, the demand for high-quality and durable crush blades is growing. Several key factors are driving this demand:
- Sustainability: There is a global push for sustainability, with businesses striving to minimize waste and reduce their environmental footprint. Efficient shredding and recycling processes, facilitated by advanced crush blades, play a crucial role in waste management and material reuse.
- Increased Automation: The rise of automation in industrial applications has led to the development of more sophisticated and efficient machinery. These systems require high-performance blades that can handle a variety of materials with minimal downtime.
- Advanced Material Requirements: As industries handle more complex and tougher materials, there is an increasing need for crush blades made from advanced materials that can withstand higher temperatures, pressures, and abrasiveness.
- Cost Efficiency: Businesses are constantly seeking ways to reduce operational costs. Long-lasting and low-maintenance crush blades contribute significantly to cost savings by reducing the need for frequent replacements and repairs.
Emerging Trends in Crush Blade Technology
The future of crush blades in industrial applications is marked by several exciting trends and innovations. These developments will improve the efficiency, lifespan, and performance of blades across various industries.
1. Advanced Material Innovations
As industries process increasingly tough materials, the need for more durable crush blades has never been greater. Traditional materials like high-carbon steel and stainless steel are being supplemented or replaced with advanced materials like tungsten carbide and ceramics. These materials offer superior wear resistance, higher strength, and better performance under extreme conditions.
For example, tungsten carbide blades are highly resistant to abrasion and are particularly effective in recycling applications where the material being processed is hard or abrasive, such as metal scraps or electronic waste. The development of new composites and alloys will continue to enhance the longevity and cutting performance of crush blades.
2. Smart Blades and IoT Integration
The integration of the Internet of Things (IoT) into industrial machinery has enabled the development of "smart" crush blades. These blades are equipped with sensors that monitor parameters like temperature, pressure, and wear in real time. By connecting these sensors to a central system, operators can predict when blades need maintenance or replacement, reducing downtime and preventing unexpected failures.
The use of IoT in crush blades also allows for more efficient energy consumption. By adjusting blade speed and cutting force based on real-time data, machines can optimize their performance, leading to energy savings and increased throughput.
3. Modular Blade Designs
In response to the diverse requirements of different industries, manufacturers are increasingly adopting modular blade designs. These blades consist of interchangeable components that can be customized to meet specific operational needs. For example, blades may be designed with different edge profiles or thicknesses depending on the material being processed.
Modular blade systems offer the advantage of easy maintenance, as individual components can be replaced or upgraded without the need to replace the entire blade assembly. This not only reduces costs but also improves machine flexibility and adaptability across multiple applications.
4. Energy-Efficient Blades
With growing emphasis on sustainability and reducing energy consumption, energy-efficient crush blades are expected to play a central role in industrial applications. By reducing friction and optimizing cutting performance, these blades can reduce the energy required to process materials, resulting in cost savings and environmental benefits.
Manufacturers are continually exploring ways to enhance blade geometry to improve cutting efficiency. The future of energy-efficient crush blades will likely include advanced aerodynamic designs that minimize energy loss and maximize cutting power.
5. Laser-Cut and Precision-Engineered Blades
Laser cutting technology is revolutionizing the manufacturing of crush blades. Laser-cut blades offer unmatched precision in their design, ensuring that the cutting edges are sharp and uniform. This precision reduces wear on the blades, enhancing their performance and longevity.
In addition, precision-engineered blades are optimized for specific applications, ensuring that they work efficiently with the materials they are designed to process. This level of customization enhances the effectiveness of the crushing process, improving both material handling and throughput.
Industries Benefiting from Advanced Crush Blade Technology
The development of advanced crush blades will have significant implications for several industries, improving efficiency, reducing operational costs, and contributing to more sustainable practices. Below are some key industries that will benefit from these innovations:
1. Recycling Industry
The recycling industry is one of the primary beneficiaries of advanced crush blade technology. As global demand for recycled materials increases, efficient processing becomes critical. Modern crush blades are essential for shredding and granulating materials like plastics, metals, rubber, and paper, making them easier to recycle.
Innovations such as smart blades and modular designs will further optimize recycling processes by reducing energy consumption, enhancing material recovery rates, and minimizing equipment downtime.
2. Waste Management
Efficient waste management is increasingly important in urban areas, where waste generation is growing at a rapid pace. Crush blades are vital for processing large volumes of household, commercial, and industrial waste, breaking down materials into smaller components for further disposal or recycling. The introduction of energy-efficient and smart blades will make waste management systems more cost-effective and environmentally friendly.
3. Agriculture and Forestry
In agriculture and forestry, crush blades are used for processing materials like tree trunks, branches, and agricultural waste. Advanced blades will improve the efficiency of chipping, mulching, and shredding operations, enabling better material reuse for composting or bioenergy production. Energy-efficient and durable blades will be particularly beneficial in large-scale operations, reducing fuel consumption and maintenance costs.
4. Manufacturing
In the manufacturing industry, crush blades are used for breaking down scrap metal, plastics, and other materials. The future of manufacturing will see more industries adopting modular and precision-engineered blades, which will offer greater flexibility and higher performance. These blades will help reduce material waste and improve production efficiency.
Table 1: Industries Benefiting from Advanced Crush Blades
Industry | Application | Benefit |
---|---|---|
Recycling | Shredding plastic, metal, and paper materials | Improved material recovery, energy savings |
Waste Management | Processing household and commercial waste | Cost-effective, reduced downtime |
Agriculture & Forestry | Shredding wood, branches, and agricultural waste | Increased efficiency, better material reuse |
Manufacturing | Breaking down scrap materials | Reduced waste, improved production rates |
Challenges and Opportunities
While the future of crush blades is promising, several challenges must be addressed:
- Cost of Advanced Materials: High-performance materials like tungsten carbide can be expensive. Manufacturers must balance the cost of advanced materials with the benefits they provide in terms of blade longevity and cutting efficiency.
- Maintenance and Replacement: Although technological advancements will reduce maintenance requirements, the wear and tear on crush blades in heavy industrial operations is inevitable. Developing cost-effective solutions for blade maintenance and replacement is crucial.
Despite these challenges, the opportunities for innovation are vast. As technology continues to advance, the future of crush blades will see even greater improvements in efficiency, sustainability, and performance.
Conclusion
The future of crush blades in industrial applications is bright, with exciting developments on the horizon. From advanced materials and energy-efficient designs to IoT integration and smart blades, the next generation of crush blades will help industries achieve higher productivity, reduced operational costs, and a lower environmental footprint.