In the world of industrial machinery, machine knives are indispensable for achieving precision cuts in various applications, from food processing to woodworking and metalworking. Over time, even the best quality knives lose their sharpness due to constant use, affecting performance and efficiency. Regular maintenance and sharpening of industrial machine knives are crucial to ensure optimal functionality, reduce operational downtime, and extend the lifespan of your equipment.
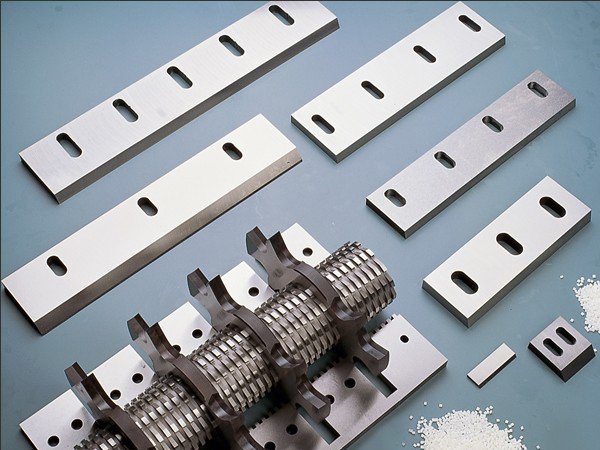
This comprehensive guide will explore the importance of sharpening industrial machine knives, the various types of machine knives, effective sharpening techniques, and best practices to achieve high-quality results every time.
The Importance of Regular Maintenance and Sharpening of Industrial Machine Knives
Industrial machine knives perform a wide range of tasks depending on their application, and they are critical for achieving the desired results in manufacturing. Whether used in cutting, slitting, slicing, or grinding, machine knives must remain sharp to perform at their best.
Why is sharpening industrial machine knives important?
- Efficiency: Dull knives require more force to cut through materials, leading to increased energy consumption and reduced productivity.
- Quality of Cut: A sharp blade provides clean, smooth cuts, which is especially important in industries like food production and packaging where consistency is key.
- Machine Wear and Tear: Dull blades put extra strain on the machinery, causing increased wear on motors and other components.
- Safety: A dull knife is more likely to slip or cause accidents. Keeping blades sharp minimizes the risk of injury.
Types of Industrial Machine Knives
Industrial machine knives come in various shapes and sizes, depending on the specific needs of the industry. Here are some common types of machine knives:
Knife Type | Application | Material |
---|---|---|
Straight Blades | Cutting through paper, plastic, or textiles | High-carbon steel, Stainless steel |
Circular Blades | Food processing, slitting operations | Tungsten carbide, High-speed steel |
Guillotine Blades | Paper cutting, textile trimming | Tool steel, Alloy steel |
Segmented Blades | Slitting, packaging, and laminating | High-carbon steel, Ceramic |
1. Straight Blades
Straight blades are one of the most common types of industrial machine knives. These are often used in applications like paper cutting, textile processing, and plastic slitting. Straight blades typically offer a long, continuous cutting edge that allows for consistent, efficient performance.
2. Circular Blades
Circular machine knives are used in a wide variety of applications, including food processing, packaging, and plastic cutting. Their round shape allows for high-speed cutting, and they can be either serrated or smooth-edged depending on the material being processed.
3. Guillotine Blades
Guillotine blades are commonly used for cutting thick materials such as cardboard and paper in industrial machines. These blades typically require high-quality, durable materials like tool steel to withstand the pressures of heavy-duty cutting.
4. Segmented Blades
Segmented blades are ideal for slitting and laminating operations. These knives consist of segments that can be replaced individually, offering a cost-effective solution for industries with frequent blade changes.
Sharpening Techniques for Industrial Machine Knives
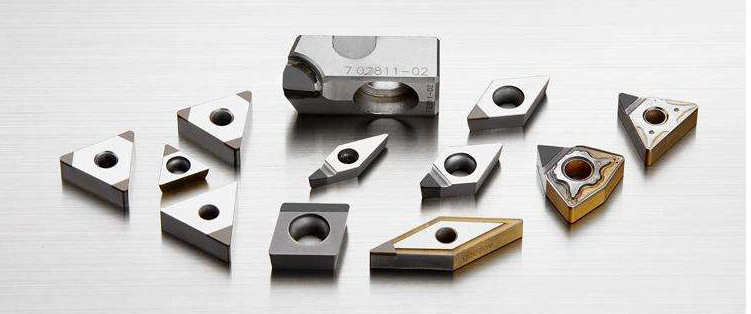
Sharpening industrial machine knives requires the right equipment and technique to ensure the blades remain effective without damaging the material. Let’s look at some of the most common sharpening methods:
1. Flat Grinding
Flat grinding involves using a rotating grinding wheel to sharpen the surface of a straight-edged knife. This technique is ideal for industrial knives with long, flat edges, such as those used in paper cutting and slitting operations.
Advantages of flat grinding:
- Precision edge maintenance.
- Consistent sharpening with minimal material removal.
- Ideal for large-scale operations.
2. Rotary Grinding
For circular machine knives, rotary grinding is the preferred method. The blade is mounted on a rotating platform, and a grinding wheel is used to refine the cutting edge.
Benefits of rotary grinding:
- Ideal for knives with circular blades.
- Delivers a sharp and clean cutting edge.
- Reduces heat buildup during the sharpening process.
3. Manual Sharpening
While manual sharpening is less common in large-scale operations, it can still be an effective solution for smaller knives or occasional maintenance. Manual sharpening involves using sharpening stones or honing rods to maintain the blade’s sharpness.
Pros of manual sharpening:
- Low cost and flexibility.
- Suitable for less frequent sharpening tasks.
- Does not require specialized machinery.
4. Automated Sharpening Machines
For large industrial operations, automated sharpening machines are ideal. These machines can handle high volumes of sharpening, maintaining consistent results and reducing manual labor. Automated machines are typically used for circular knives, planer knives, and other high-precision blades.
Advantages:
- High-speed sharpening.
- Minimal human intervention required.
- Accurate and consistent results.
Tips for Achieving Optimal Results when Sharpening Industrial Machine Knives
Achieving the best possible sharpness for your industrial machine knives requires attention to detail and proper technique. Here are some essential tips for sharpening industrial knives effectively:
Tip | Explanation |
---|---|
Choose the Right Grinding Wheel | Select a grinding wheel that matches the material of the knife to avoid overheating or damaging the blade. |
Monitor Blade Temperature | Overheating can weaken the steel of the knife. Use coolant or take breaks to keep the blade cool. |
Inspect Blades Regularly | Look for cracks, chips, or any signs of excessive wear. Dull blades are a sign that it’s time to sharpen them. |
Maintain Consistent Pressure | Apply even pressure during sharpening to ensure a smooth and uniform edge. |
Use a Polishing Step | After sharpening, use a polishing process to remove burrs and refine the edge, making the knife last longer. |
Signs It’s Time to Sharpen Your Industrial Machine Knives
It’s important to monitor the performance of your knives so you can sharpen them before they start affecting your production. Here are some signs that your industrial machine knives need sharpening:
- Reduced Cutting Performance: If you notice an increase in energy consumption or slower cutting speeds, it’s likely your knives have lost their sharpness.
- Rough Cuts: If the cuts are becoming jagged or uneven, it’s time to sharpen the knives.
- Excessive Wear on Other Machine Parts: Dull knives cause the machine to work harder, which increases the wear on motors, bearings, and other components.
- Frequent Adjustments: If you need to adjust the machine frequently to maintain performance, your knives may need sharpening.
Conclusion: The Value of Sharpening Industrial Machine Knives
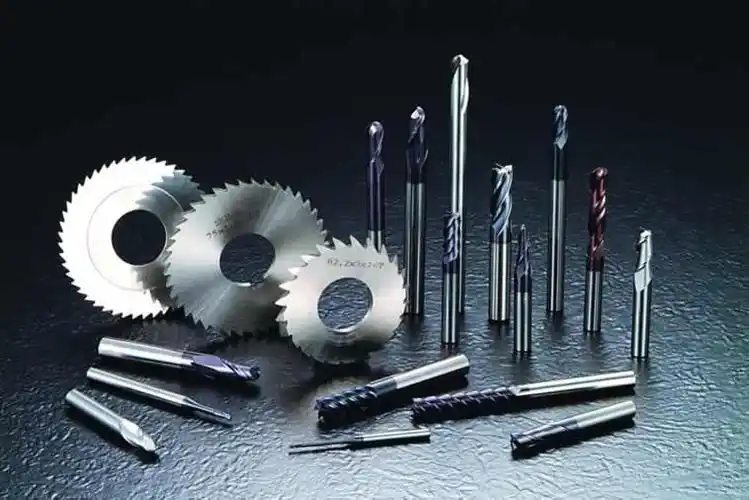
Regular sharpening and maintenance of industrial machine knives are vital to maintaining operational efficiency, ensuring safety, and producing high-quality products. By choosing the right sharpening method and implementing a consistent maintenance routine, you can extend the life of your blades, improve machine performance, and reduce the overall cost of operations.
From flat grinding to automated sharpening, there are various methods available to suit the specific needs of your operation. By staying vigilant about the condition of your knives and sharpening them at the right intervals, you’ll keep your machines running smoothly and efficiently, ensuring you get the best results every time.