Provide high-precision and high-quality products
MISIQI Machinery Technology
Get to know our company faster.
Company Profile
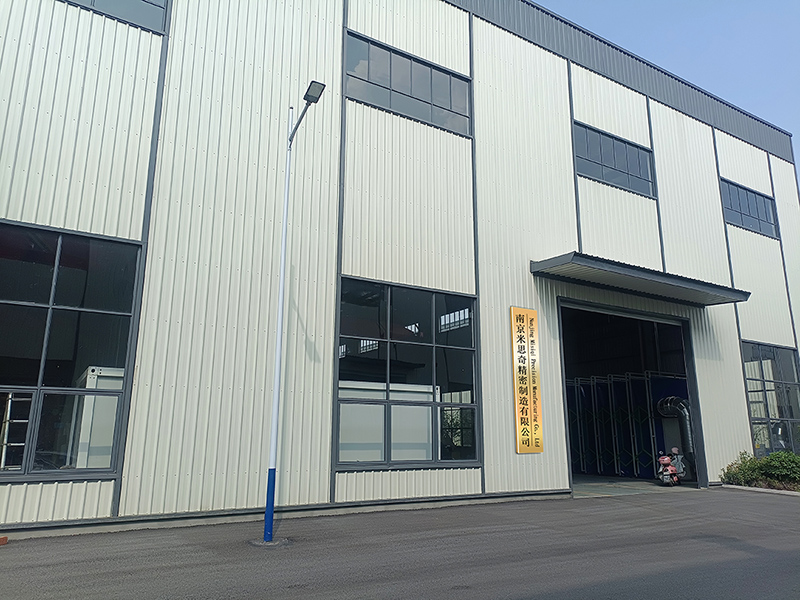
-
Customized
More than a dozen kinds of products, thousands of different specifications, support a variety of sizes of material style custom processing.
-
20years+
With more than 20 years of experience, we have rich experience in production and custom processing to give customers the best products and services.
-
Process
There are more than 20 kinds of processing technology, and the production process is strictly controlled to ensure product quality.
High Precision from MISIQI
The company insists on giving customers the best service, and we will give customers suitable procurement suggestions according to the actual production needs of customers, and then provide high-precision and high-quality products.
Company business scope
Company business scope
-
Tailored to customer requirements
We customize our products to meet your specific needs. Using special hardening processes, optimizing geometries, changing materials, or implementing special cutter angle specifications, ` ensure that each knife is perfectly suited to your requirements.
-
Sketch
Provide us with a sketch detailing the desired shape and dimensions of the knife. Following this, we'll engage in discussions with you to gather any additional necessary information.
-
Specimen Reproduction
We accurately reproduce specimens provided by customers. To achieve this, we analyze the material composition and test the hardness to ensure exact replication.
-
Drawing
We manufacture your knife precisely following your specifications. You have the option to base tolerances on industry standards or define your own custom tolerances.
-
Problem Analysis and Output Optimization
At our company or at your facilities, we work closely with you to identify problems and propose solutions to enhance cutting performance. This may involve modifying materials, adjusting angles, optimizing shapes, applying coatings, or polishing techniques. Our goal is to improve efficiency and output while resolving any issues encountered.
-
Reasonable Price
With over 10 precision production lines, we can easily produce large quantities of goods, allowing us to offer competitive pricing. Our commitment to efficiency enables us to provide you with the best possible price.
Enterprise Advantage Display
Enterprise Advantage Display
-
Quality and Consistency
ISO 9001:2015, ISO 13485:2016 certified
Automatic in-process measurement of key parameters
Batch tracking: if required, each blade can be marked with a unique serial number -
Expertise and Experience
In-house tool & die shop and metallurgy laboratory
CAD-based development and Rapid Prototyping
Cooperation with leading users and research institutes
Almost 20+ years of experience -
Your Productivity and Efficiency
Increased blade durability and reduced retooling times
Measurably increased machine up-times
Excellent cutting quality, less post-production checking
Higher yield per slice
Company environment
provide high-precision and high-quality products
Choose Our Strengths
-
Abundant Production Experience
About 20 year's experience, choose the most suitable products for you.
-
Professional Technical Team
Professional engineer give the technical supports, The superb Heat treatment technology ensures the high quality of the products
-
Experienced and Responsible Workers
Put every effort and attention to produce the best products
-
High Accuracy Equipment
Make sure the blades in high accuracy and high precision. The thickness is in 0.002mm, always at 0mm.
Frequently asked questions are answered immediately
FAQ Answer Questions Quickly
-
01
Frequently Asked Questions (FAQs)
We offer a wide range of products, including food processing knives, industrial cutting tools, and specialized blades for various applications. Our product line includes knives for bakery and pastry, meat processing, fruit and vegetable processing, as well as blades for ceramics, printing machinery, and papermaking.
-
02
What materials are your products made from?
Our products are made from high-quality materials such as:
Stainless Steel: Rust-resistant and food-safe, ideal for food processing and industrial applications.
Ceramic: Lightweight and extremely sharp, suitable for precision cutting.
High-Carbon Steel: Offers excellent edge retention but requires more maintenance, ideal for professional use. -
03
Can I customize the dimensions and design of the products?
Yes, we offer customization options for blade length, width, thickness, and edge profiles. You can also choose the handle material and design to suit your specific needs. Simply provide us with your specifications or a sketch, and we will tailor the products to your requirements.
-
04
How do you ensure the quality of your products?
We adhere to strict quality control standards, including ISO 9001:2015 and ISO 13485:2016 certifications. We use automatic in-process measurement for key parameters and batch tracking to ensure consistency and traceability. Each product undergoes rigorous testing to meet high performance and safety standards.
-
05
Are your products suitable for industrial use?
Absolutely. Our products are designed for various industrial applications, including food processing, ceramics, printing machinery, and papermaking. They are built to withstand heavy use and maintain their performance over time.
-
06
What is the lead time for custom orders?
The lead time for custom orders depends on the complexity and quantity of the order. Typically, it ranges from 2 to 4 weeks. We will provide you with a specific timeline once we receive your detailed specifications and approve the prototype.
-
07
Do you offer any warranties or guarantees?
Yes, we offer a warranty on our products to ensure customer satisfaction. The warranty covers defects in materials and workmanship for a specified period, typically 12 months. If you encounter any issues, please contact our customer service team for assistance.
-
08
How should I maintain my products?
To ensure the longevity and performance of your products, follow these maintenance tips:
Clean the products thoroughly after each use to prevent residue buildup.
Store the products in a dry place to avoid rust.
Sharpen the blades regularly using a suitable honing tool.
Avoid dropping or mishandling the products to prevent damage. -
09
Can you provide samples for testing?
Yes, we can provide samples for testing upon request. Please contact our sales team to discuss your requirements and arrange for sample delivery.
-
10
What is the minimum order quantity (MOQ)?
The minimum order quantity varies depending on the type of product and customization level. For standard products, the MOQ is typically 100 units, while for custom products, it may be higher. We can discuss the specific MOQ with you during the consultation process.
-
11
Do you offer international shipping?
Yes, we offer international shipping to ensure our products reach customers worldwide. Shipping costs and delivery times will vary based on your location. Contact us for a shipping quote and estimated delivery time.
If you have any further questions or need more information, please feel free to contact our customer service team. We are here to help!