Industrial knives are tools designed to tackle cutting tasks for metals and a variety of other materials. They are utilized across diverse industries, including food processing, metalworking, woodworking, and manufacturing. These knives are commonly employed in factories and large-scale processing facilities.
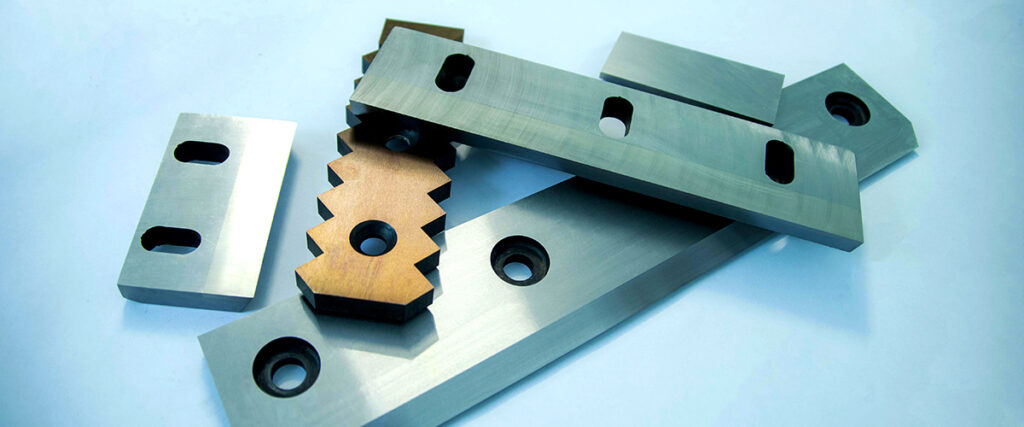
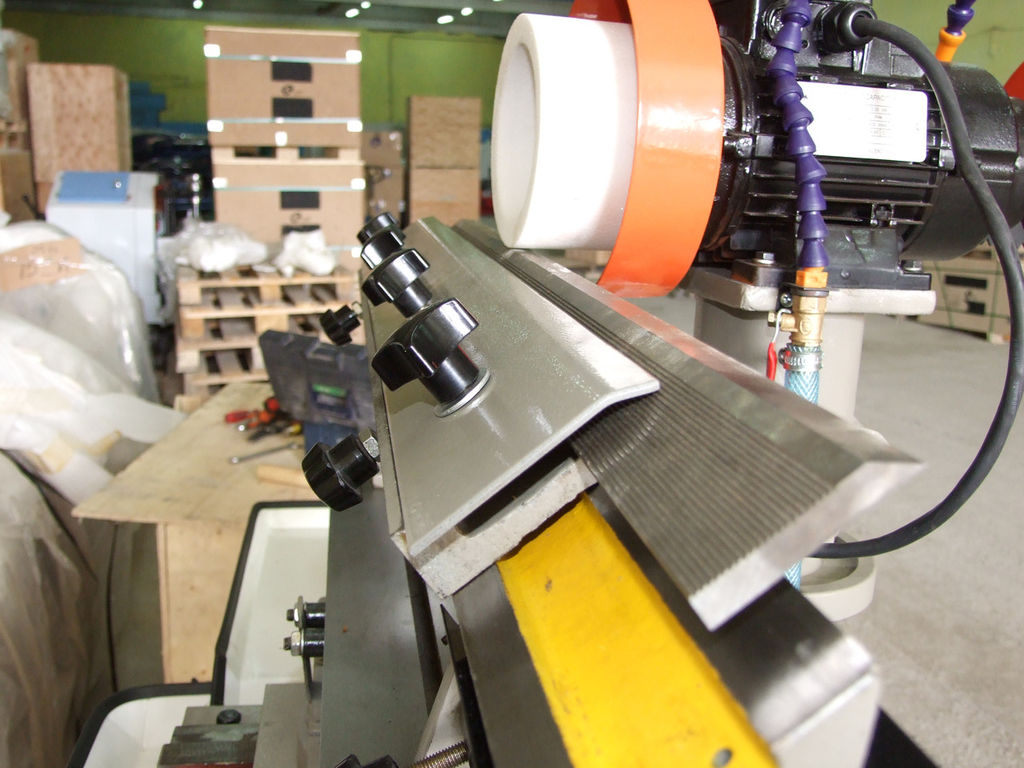
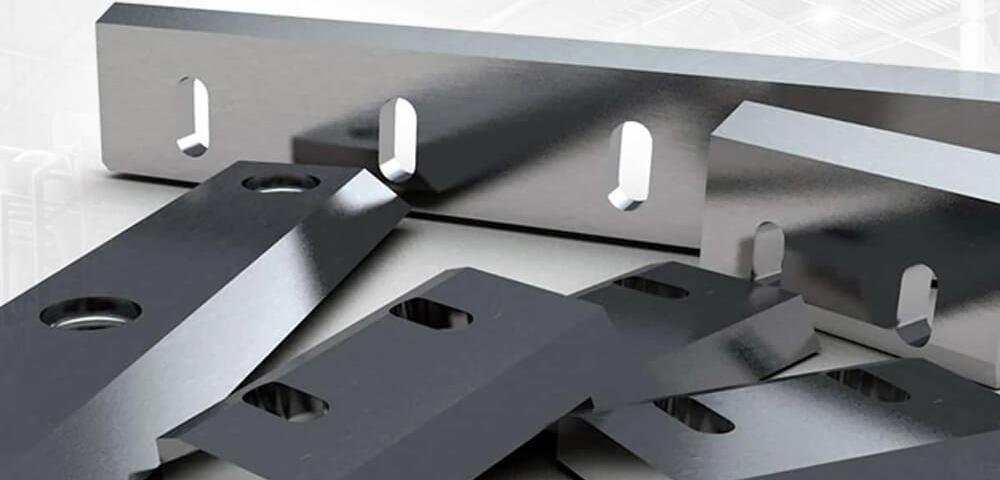
Types of Industrial Knives
- Crusher Knives: Industrial knives for crushers are used in machines to grind various materials such as plastic, rubber, wood, and metal. These knives must be durable and wear-resistant, as they handle high loads and abrasive materials.
- Facas de guilhotina: Guillotine knives are employed in machines for cutting sheet materials like metal, paper, cardboard, and plastic. They ensure a straight and clean cut, which is essential for precise and neat material processing.
- Chopping Knives: Chopping knives are used in chopping machines to break down wood into smaller particles. They are often utilized in the production of wood chips and other wood products. These knives need to be exceptionally strong and sharp to effectively process hard wood.
- Facas de descascar: Peeling knives are designed to remove bark or a thin top layer of material, such as in plywood production. They provide precise and clean removal of a thin wood layer, which is critical for producing high-quality products.
- Planing Knives: Planing knives are used in machines to plane wood, removing a thin layer of material to achieve the desired shape and smoothness. These knives must be extremely sharp and wear-resistant.
- Facas de disco: Disc knives are circular blades that cut various materials while rotating. They are primarily used in the production of paper, film, textiles, and metal, offering a continuous and uniform cut.
- Die-Cutting Knives: Die-cutting knives are used in die-cutting presses to cut shaped parts from sheet materials such as metal, plastic, cardboard, and textiles. These knives enable the creation of complex shapes with high precision.
- Toothed Knives: Toothed knives feature a serrated cutting edge and are used for cutting materials that are challenging to process with standard knives, such as bread, foam, rubber, and other soft or fibrous materials.
- Segmented Knives: Segmented knives have a segmented cutting surface and are used for cutting materials requiring high precision. They are commonly found in industries like paper and plastic production.
- Disc-Shaped Knives: Disc-shaped knives have a plate-like design and are used in specialized machines for cutting and grinding. Their structure ensures high strength and efficiency when processing various materials.
Each type of knife has unique characteristics and purposes, making them indispensable in various industrial processes.
Manufacturing Stages and Technology
Industrial knives play a pivotal role in numerous production processes, ensuring precision and efficiency in cutting, crushing, and material processing. The manufacturing process typically involves several critical stages and the application of advanced technologies. Below, we explore the main stages and technological processes involved in producing industrial knives.
Stages of Manufacturing Industrial Knives
- Seleção de materiais: The first and most vital stage is selecting the material for the knives. Industrial knives are generally made from high-carbon steels, stainless steels, alloy steels, or special alloys with high hardness and wear resistance. The material choice depends on the knife’s intended use and operating conditions.
- Design and Development: During this stage, design engineers create blueprints and 3D models of the future knife. Modern design technologies, such as CAD (Computer-Aided Design), enable the development of precise models that meet all requirements and parameters. Key considerations include the knife’s geometry, balance, sharpening angle, and other factors affecting performance and durability.
- Cutting Blanks: Once the design is approved, the process of cutting blanks from the chosen material begins. Laser, plasma, or waterjet machines are used to ensure high precision and clean cuts. This stage produces blanks of the required shape and size for further processing.
- Tratamento térmico: Heat treatment is a crucial step in manufacturing industrial knives. It involves hardening, tempering, and sometimes additional aging. Hardening increases the steel’s hardness for better wear resistance, while tempering reduces brittleness and enhances strength. This process occurs in specialized furnaces with precise temperature and timing control.
- Mechanical Processing: At this stage, blanks undergo mechanical processing on lathes, milling machines, and grinders. This includes turning, milling, drilling, and grinding, with special attention given to the cutting edge, which must be perfectly sharp and even. High-precision grinding and sharpening machines ensure micron-level accuracy.
- Sharpening and Finishing: Sharpening is a key stage that determines the knife’s operational efficiency. It involves multiple steps, from rough sharpening to fine finishing. Special abrasive wheels and pastes are used to achieve optimal sharpness and smoothness. Some knives may also require polishing to enhance corrosion resistance and improve appearance.
- Controle de qualidade: After processing, the knives undergo rigorous quality checks, including assessments of geometric parameters, hardness, strength, and sharpness. High-precision measuring tools and test benches are used, and only knives passing all tests proceed to packaging and shipment.
- Packaging and Shipping: The final stage involves packaging the finished knives to protect them from mechanical damage and corrosion during transport and storage. Once packaged, the knives are shipped to customers or stored in warehouses.
Modern Technologies and Innovations
Modern technologies and innovations significantly enhance industrial knife production. The use of new materials, advanced heat treatment methods, automation, and robotics improves quality and productivity. Computer modeling and numerical control (CNC) ensure high precision and repeatability, particularly in mass production.
In conclusion, manufacturing industrial knives is a complex, multi-stage process requiring a high level of expertise and cutting-edge technology. A meticulous approach at every stage ensures the creation of knives that meet stringent standards and perform effectively under demanding conditions.
Materials for Manufacturing
The production of knives is both an art and a science, with material selection determining their durability, efficiency, and application scope. Different steel types offer unique properties tailored to specific tasks:
- For Working with Light Materials:
- Bearing Structural Steel SUJ2: Ideal for knives cutting paper, cardboard, and other materials that don’t require high strength or wear resistance.
- Alloy Tool Steel 9CrSi: Suitable for knives cutting soft materials like wood.
- Carbon Tool Steel SK5: Known for its elasticity, it’s appropriate for cutting plastic, polyethylene, and soft metals.
- For More Complex Tasks:
- Corrosion-Resistant Stainless Steels like SUS420: Perfect for aggressive environments and food production, with high hardness (55 HRC) and oxidation resistance up to +450°C, making them ideal for repeated use.
- Die Tool Steel SKD-11: Offers excellent wear resistance, making it suitable for guillotine knives in harsh conditions.
- High-Speed Tool Steel HSS: Leads in wear resistance and is capable of cutting various metals.
Key factors in steel selection:
- Dureza: Determines cutting ability and service life.
- Resistência ao desgaste: Resistance to damage and deformation during use.
- Elasticity: Ability to return to its original shape after deformation.
Choosing the right steel is critical for ensuring the efficiency and longevity of industrial knives.
Application Areas
Industrial knives are essential tools across a wide range of industries. Their rigidity and strength vary based on task requirements, allowing for tailored solutions for specific jobs.
For instance, in the paper industry, disc cutting tools are widely used for precise and efficient material processing. In metalworking, guillotine knives excel at handling high-strength materials.
Toothed knives, featuring sharpened metal blades, are employed for separating polymers or fabrics, ensuring smooth and clean cuts.
Industrial knives are actively used in fields such as packaging equipment, metal cutting machinery, and industrial meat grinders, showcasing their versatility and reliability across diverse production sectors.
Features of Knife Operation
The technology of separation transitions used in material cutting has distinct characteristics. A key factor is the rapid penetration of the cutting tool into the material’s structure, leading to increasing force loads. Unlike other methods, there is no stationary phase where the load remains constant. After reaching a peak, the force drops sharply, accompanied by material fracture through splitting or plastic shear.
The final stage involves pushing through the cut section, requiring a renewed increase in force to overcome friction and remove material remnants.
The process varies depending on the material. For heated blanks, especially those made of high-carbon steels, this technology is less effective, and alternative separation methods are recommended.
Resistance during material separation depends on:
- Specific Cutting or Shearing Force: The force required per unit area to separate the material.
- Velocidade de corte: The speed at which the cutting tool moves.
- Nominal Gap: The distance between the cutting edge and the material.
- Material Thickness: The amount of material to be cut.
- Plastic Characteristics: Relative penetration and deformation properties affecting material behavior under load.
The operation process can be divided into five stages:
- Elastic Compression: The load from the cutting tool does not exceed the material’s shear strength, with no visible changes in cross-section or appearance.
- Plastic Penetration: Begins when the cutting edge surpasses the material’s strength limit, causing layer shear and peak force.
- Fracture: Cracks form and spread from the edge inward, following stress concentration points and the path of least resistance, reducing the force.
- Complete Separation: The cut section fully detaches, with force decreasing due to friction.
- Pushing Through: A final minor force removes the cut piece.
For brittle or soft materials like plastic, separation occurs continuously without impact effects.
Note that this is a generalized description of separation transition technology. Specific implementations may vary based on equipment, material type, and other factors.
Manufacturing Knives According to Drawings
Industrial knives are typically custom-made based on customer drawings or sketches. Whether for metal cutting or woodworking machines, the drawing specifies all necessary parameters, shapes, and configurations. However, some customers request knives based on a sample, which may result in less precision compared to drawing-based production—a factor to consider.