Machine knives for steel are specialized cutting tools designed to handle the high strength and durability of steel materials. These knives are crucial in industries that process steel, including manufacturing, construction, recycling, and metalworking. Steel, being a robust and often hard material, requires knives that offer precision, reliability, and long-lasting performance. This article will explore machine knives for steel from various perspectives, including types, applications, material considerations, maintenance, installation, and troubleshooting.
1. Applications of Machine Knives for Steel
Machine knives for steel are used in a variety of processes within industries that involve steel cutting, shaping, and processing. These applications typically require high-performance knives capable of withstanding high stresses, wear, and temperatures.
1.1. Steel Plate Cutting
Steel plates are often used in industries such as automotive, shipbuilding, and construction. Machine knives designed for cutting steel plates must be able to handle thick and hard materials. The cutting process can be done using guillotine knives or rotary knives, depending on the requirements for precision and the thickness of the steel.
1.2. Steel Strip Cutting
In steel mills, machine knives are used to cut steel strips into different sizes. This process is often a part of continuous rolling mills where large rolls of steel are transformed into strips. Steel strip knives need to have precise cutting edges to ensure that the steel is cut cleanly and accurately, minimizing material waste.
1.3. Steel Shearing
In shearing applications, machine knives are used to cut steel sheets, bars, and other forms of steel into smaller sections. The shear knives must have high tensile strength to resist the force generated during the shearing process, ensuring smooth cuts without burrs or cracks. This application is common in metal processing plants, recycling centers, and fabrication shops.
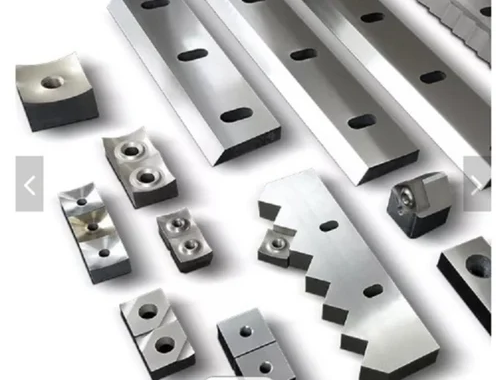
1.4. Steel Recycling
Steel recycling requires powerful machines to shred and process scrap steel. Shredder knives are commonly used in these applications. The knives must be durable enough to handle tough and often irregularly shaped scrap steel, including beams, car parts, and old appliances. These knives play a critical role in breaking down the scrap into smaller pieces, which can then be melted down and repurposed.
1.5. Steel Slitting
Steel slitting involves cutting a large roll of steel into narrower strips. Slitting knives are used to create uniform widths and smooth edges. These knives are designed to handle the hardness and toughness of steel while delivering precise, straight cuts. The process requires high-speed cutting with minimal deformation of the material.
2. Types of Machine Knives for Steel
There are various types of machine knives, each suited for specific tasks in steel processing. These knives are engineered to meet the demanding needs of steel cutting, which requires precision, strength, and durability.
Tipo de cuchillo | Solicitud | Características principales |
---|---|---|
Cuchillos de guillotina | Used in plate cutting and shearing processes. | Straight-edge knives for high-force cutting. |
Cuchillas rotativas | Used for slitting steel rolls into narrow strips. | Circular blades for high-speed cutting. |
Cuchillas trituradoras | Used in steel recycling. | Heavy-duty knives for shredding scrap steel. |
Cuchillos de corte | Used in steel slitting. | Blades for precise, narrow cuts in continuous rolls. |
Hacksaw Blades | Used in manual and automated sawing of steel bars. | Thin, flexible blades for cutting through steel rods and bars. |
3. Material Considerations
The material used to manufacture machine knives for steel plays a critical role in determining the knife's performance and lifespan. Steel itself is a challenging material to cut, and the knives must be made from materials that are harder and more durable than the material they are cutting.
3.1. High-Speed Steel (HSS)
High-speed steel is a common material used for manufacturing machine knives for steel. HSS has excellent hardness and wear resistance, making it ideal for cutting through tough materials like steel. It also retains its hardness at high temperatures, which is beneficial in processes that generate significant heat during cutting.
3.2. Tungsten Carbide
Tungsten carbide is another material frequently used for machine knives. Tungsten carbide knives offer exceptional hardness, wear resistance, and the ability to cut through even the toughest steel. Tungsten carbide knives are often used in heavy-duty applications, such as shredding scrap metal, and are known for their long-lasting durability.
3.3. Tool Steel
Tool steel is used for knives that require a balance of hardness and toughness. It is often used in knives designed for general-purpose steel cutting, such as those in shearing and slitting applications. Tool steel knives tend to offer a good mix of durability, edge retention, and toughness.
3.4. Stainless Steel
Stainless steel knives are used in applications where corrosion resistance is necessary, such as in environments with moisture or where steel cutting may involve exposure to chemicals. These knives maintain sharpness and provide good resistance to rust, which can prolong their lifespan.
4. Installation of Machine Knives for Steel
Correct installation is crucial for ensuring the longevity and performance of machine knives for steel. Improper installation can lead to increased wear, vibration, misalignment, and other operational issues.
4.1. Preparation and Inspection
Before installing a new knife, inspect it for any defects, cracks, or imperfections. Ensure that the knife is the correct size and type for your specific machine and application. Additionally, ensure that the machine is clean and free from debris, as any foreign material could affect the performance of the knife.
4.2. Alignment
Proper alignment of the knife with the machine is crucial to achieving precise cuts and preventing unnecessary wear. The knife should be installed in such a way that it maintains a consistent cutting edge angle. If the knife is misaligned, it may cause uneven cuts and premature wear on both the knife and the machine.
4.3. Secure Mounting
Once aligned, the knife should be secured tightly to the machine’s cutting assembly. Ensure that all bolts or fasteners are tightened evenly to avoid stressing the knife unevenly. Over-tightening may lead to knife distortion, while under-tightening could result in the knife becoming loose during operation.
5. Maintenance of Machine Knives for Steel
The longevity of machine knives for steel depends largely on regular maintenance. Without proper care, knives can degrade rapidly due to the tough nature of steel. Proper maintenance practices ensure that knives maintain their cutting efficiency and performance over time.
5.1. Regular Inspection
Regularly inspecting machine knives is essential to identify any damage, wear, or build-up of material that could hinder their performance. Check for signs of cracks, chips, dullness, or burrs. Dull knives should be sharpened promptly to avoid increased stress on the machine and reduced cutting quality.
5.2. Sharpening
Sharpening machine knives for steel is crucial for maintaining cutting efficiency. Knives that have become dull will require more force to cut, which can lead to increased wear on both the knives and the machine. Specialized sharpening equipment is used to restore the knife's edge, ensuring that it continues to perform at optimal levels.
5.3. Lubrication
In some cases, lubrication is necessary to reduce friction between the knife and the material being cut. Proper lubrication reduces wear on the knife, helping it retain its sharpness longer. Be sure to use the appropriate lubricant for the specific knife and machine type to prevent corrosion and ensure smooth operation.
5.4. Cleaning
Steel cutting often results in the accumulation of metal shavings, oil, and other debris. These should be cleaned regularly from the knife surface. A buildup of debris can cause the knife to dull quickly and can even lead to damage if left unchecked.
6. Solución de problemas comunes
Even with proper maintenance, several issues can arise during the operation of machine knives for steel. Here are some common problems and their solutions:
Problema | Causa | Solución |
---|---|---|
Dull Cuts | Knife wear, improper sharpening. | Sharpen the knife and inspect for proper alignment. |
Uneven Cutting | Misalignment of the knife or worn components. | Realign the knife and replace any worn components. |
Vibración excesiva | Loose knife or incorrect mounting. | Tighten all fasteners and check alignment. |
Excessive Wear | Incorrect material or improper use. | Use the right knife material and ensure proper maintenance. |
7. Conclusión
Machine knives for steel are essential tools in a variety of steel processing applications. They are designed to cut through some of the toughest materials and require high durability and precision. By selecting the appropriate material, type, and maintenance practices, companies can ensure the longevity and performance of their knives. Proper installation, regular inspection, and sharpening are all necessary to maintain the efficiency of these critical tools.