Industriemesser sind Werkzeuge zum Schneiden von Metallen und einer Vielzahl anderer Materialien. Sie werden in verschiedenen Branchen eingesetzt, darunter in der Lebensmittelverarbeitung, Metallverarbeitung, Holzverarbeitung und Fertigung. Sie werden häufig in Fabriken und großen Verarbeitungsanlagen eingesetzt.
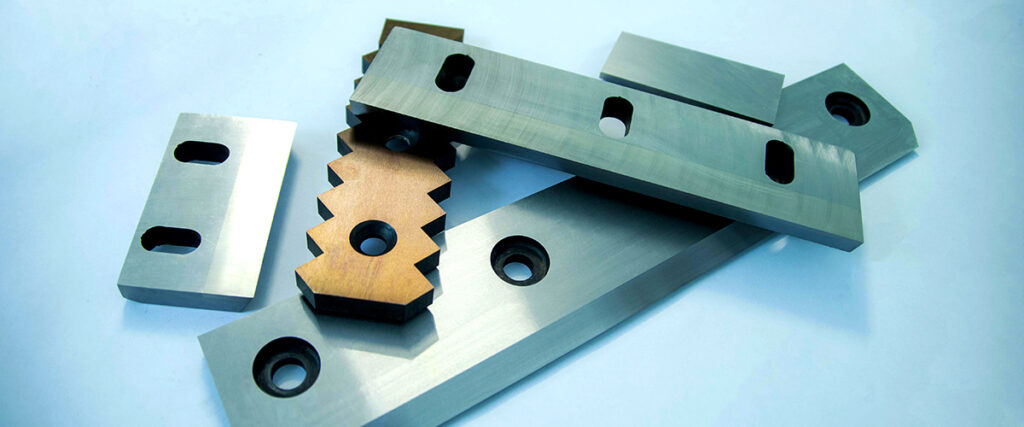
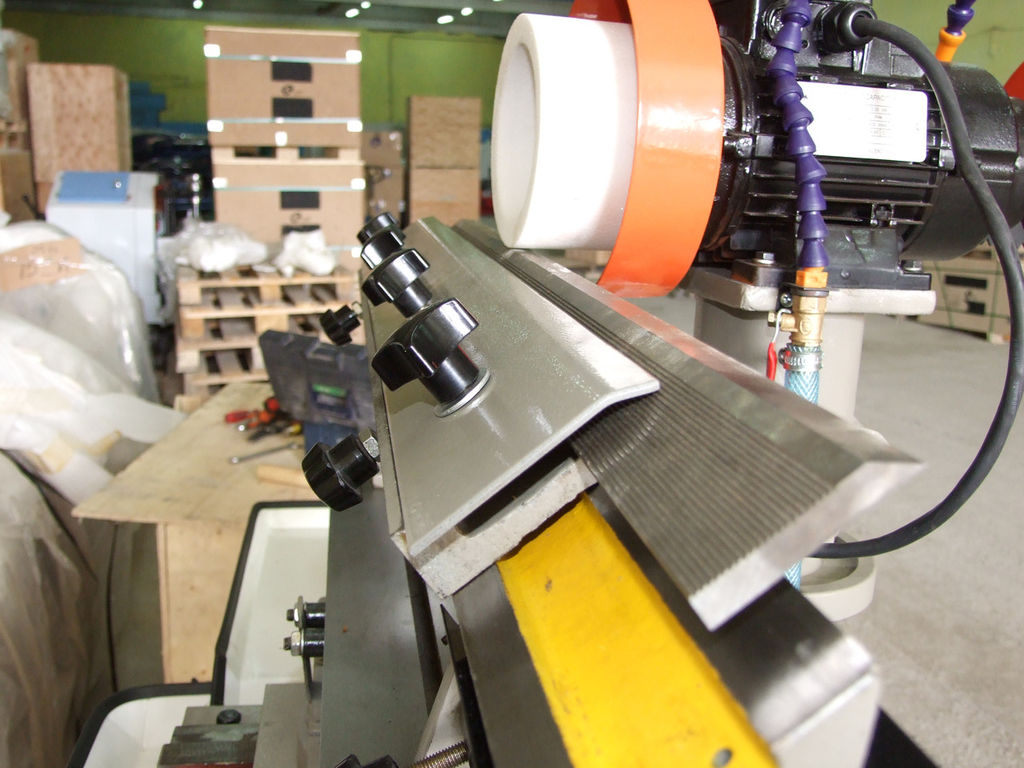
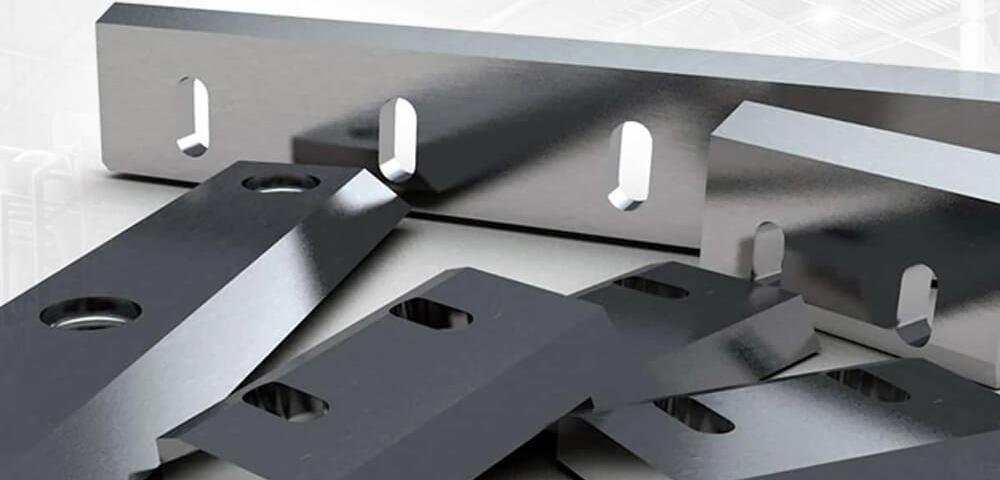
Arten von Industriemessern
- BrechermesserIndustriemesser für Brecher werden in Maschinen zum Zerkleinern verschiedener Materialien wie Kunststoff, Gummi, Holz und Metall eingesetzt. Diese Messer müssen langlebig und verschleißfest sein, da sie hohen Belastungen und abrasiven Materialien standhalten.
- GuillotinemesserGuillotinemesser werden in Maschinen zum Schneiden von Plattenmaterialien wie Metall, Papier, Karton und Kunststoff eingesetzt. Sie gewährleisten einen geraden und sauberen Schnitt, der für eine präzise und saubere Materialverarbeitung unerlässlich ist.
- HackmesserHackmesser werden in Hackmaschinen verwendet, um Holz in kleinere Partikel zu zerlegen. Sie werden häufig bei der Herstellung von Hackschnitzeln und anderen Holzprodukten eingesetzt. Diese Messer müssen außergewöhnlich stark und scharf sein, um Hartholz effektiv verarbeiten zu können.
- SchälmesserSchälmesser dienen zum Entfernen von Rinde oder dünnen Deckschichten, beispielsweise bei der Sperrholzherstellung. Sie ermöglichen das präzise und saubere Entfernen einer dünnen Holzschicht, was für die Herstellung hochwertiger Produkte entscheidend ist.
- HobelmesserHobelmesser werden in Maschinen zum Hobeln von Holz verwendet. Dabei wird eine dünne Schicht Material entfernt, um die gewünschte Form und Glätte zu erzielen. Diese Messer müssen extrem scharf und verschleißfest sein.
- ScheibenmesserScheibenmesser sind kreisförmige Klingen, die rotierende Schnitte in verschiedene Materialien ausführen. Sie werden vor allem in der Papier-, Folien-, Textil- und Metallproduktion eingesetzt und ermöglichen einen kontinuierlichen und gleichmäßigen Schnitt.
- Stanzmesser: Stanzmesser werden in Stanzpressen verwendet, um Formteile aus Plattenmaterialien wie Metall, Kunststoff, Karton und Textilien auszuschneiden. Diese Messer ermöglichen die Herstellung komplexer Formen mit hoher Präzision.
- Gezahnte Messer: Zahnmesser verfügen über eine gezackte Schneide und werden zum Schneiden von Materialien verwendet, die mit Standardmessern nur schwer zu verarbeiten sind, wie etwa Brot, Schaumstoff, Gummi und andere weiche oder faserige Materialien.
- Segmentierte MesserSegmentierte Messer haben eine segmentierte Schneidfläche und werden zum Schneiden von Materialien verwendet, die hohe Präzision erfordern. Sie werden häufig in Branchen wie der Papier- und Kunststoffproduktion eingesetzt.
- Scheibenförmige Messer: Scheibenförmige Messer haben eine plattenartige Form und werden in Spezialmaschinen zum Schneiden und Schleifen verwendet. Ihre Struktur gewährleistet hohe Festigkeit und Effizienz bei der Bearbeitung verschiedener Materialien.
Jeder Messertyp hat einzigartige Eigenschaften und Zwecke, was ihn in verschiedenen industriellen Prozessen unverzichtbar macht.
Fertigungsstufen und Technologie
Industriemesser spielen in zahlreichen Produktionsprozessen eine zentrale Rolle und gewährleisten Präzision und Effizienz beim Schneiden, Zerkleinern und der Materialbearbeitung. Der Herstellungsprozess umfasst typischerweise mehrere kritische Phasen und den Einsatz fortschrittlicher Technologien. Im Folgenden untersuchen wir die wichtigsten Phasen und technologischen Prozesse der Herstellung von Industriemessern.
Phasen der Herstellung von Industriemessern
- MaterialauswahlDer erste und wichtigste Schritt ist die Auswahl des Messermaterials. Industriemesser werden in der Regel aus Kohlenstoffstahl, rostfreiem Stahl, legiertem Stahl oder Speziallegierungen mit hoher Härte und Verschleißfestigkeit hergestellt. Die Materialwahl hängt vom Verwendungszweck und den Betriebsbedingungen des Messers ab.
- Design und Entwicklung: In dieser Phase erstellen Konstrukteure Entwürfe und 3D-Modelle des zukünftigen Messers. Moderne Konstruktionstechnologien wie CAD (Computer-Aided Design) ermöglichen die Entwicklung präziser Modelle, die alle Anforderungen und Parameter erfüllen. Wichtige Aspekte sind die Geometrie, Balance, der Schärfwinkel und weitere Faktoren, die Leistung und Haltbarkeit des Messers beeinflussen.
- ZuschnitteSobald das Design freigegeben ist, beginnt der Prozess des Zuschneidens der Rohlinge aus dem gewählten Material. Laser-, Plasma- oder Wasserstrahlmaschinen sorgen für hohe Präzision und saubere Schnitte. In diesem Schritt werden Rohlinge in der gewünschten Form und Größe für die Weiterverarbeitung hergestellt.
- WärmebehandlungDie Wärmebehandlung ist ein entscheidender Schritt bei der Herstellung von Industriemessern. Sie umfasst Härten, Anlassen und manchmal zusätzliches Altern. Das Härten erhöht die Härte des Stahls und sorgt so für eine bessere Verschleißfestigkeit, während das Anlassen die Sprödigkeit verringert und die Festigkeit erhöht. Dieser Prozess findet in Spezialöfen mit präziser Temperatur- und Zeitkontrolle statt.
- Mechanische Bearbeitung: In dieser Phase werden die Rohlinge auf Dreh-, Fräs- und Schleifmaschinen mechanisch bearbeitet. Dazu gehören Drehen, Fräsen, Bohren und Schleifen. Besonderes Augenmerk gilt dabei der Schneide, die perfekt scharf und eben sein muss. Hochpräzise Schleif- und Schärfmaschinen gewährleisten eine Genauigkeit im Mikrometerbereich.
- Schärfen und FinishenDas Schärfen ist ein entscheidender Schritt, der die Leistungsfähigkeit des Messers bestimmt. Es umfasst mehrere Schritte, vom Grobschliff bis zum Feinschliff. Spezielle Schleifscheiben und -pasten sorgen für optimale Schärfe und Glätte. Manche Messer müssen zusätzlich poliert werden, um die Korrosionsbeständigkeit zu erhöhen und das Aussehen zu verbessern.
- Qualitätskontrolle: Nach der Verarbeitung werden die Messer strengen Qualitätskontrollen unterzogen, darunter die Bewertung geometrischer Parameter, Härte, Festigkeit und Schärfe. Es kommen hochpräzise Messwerkzeuge und Prüfstände zum Einsatz. Nur Messer, die alle Tests bestehen, werden verpackt und versendet.
- Verpackung und Versand: Im letzten Schritt werden die fertigen Messer verpackt, um sie während Transport und Lagerung vor mechanischen Beschädigungen und Korrosion zu schützen. Nach der Verpackung werden die Messer an Kunden versandt oder in Lagerhallen eingelagert.
Moderne Technologien und Innovationen
Moderne Technologien und Innovationen verbessern die industrielle Messerproduktion erheblich. Der Einsatz neuer Materialien, fortschrittlicher Wärmebehandlungsverfahren, Automatisierung und Robotik steigert Qualität und Produktivität. Computermodellierung und numerische Steuerung (CNC) gewährleisten hohe Präzision und Wiederholgenauigkeit, insbesondere in der Massenproduktion.
Zusammenfassend lässt sich sagen, dass die Herstellung von Industriemessern ein komplexer, mehrstufiger Prozess ist, der ein hohes Maß an Fachwissen und modernste Technologie erfordert. Ein sorgfältiger Ansatz in jeder Phase gewährleistet die Herstellung von Messern, die strengen Standards entsprechen und unter anspruchsvollen Bedingungen effektiv funktionieren.
Materialien für die Fertigung
Die Herstellung von Messern ist Kunst und Wissenschaft zugleich. Die Materialauswahl bestimmt Haltbarkeit, Effizienz und Einsatzmöglichkeiten. Verschiedene Stahlsorten bieten einzigartige Eigenschaften, die auf spezifische Aufgaben zugeschnitten sind:
- Für die Bearbeitung leichter Werkstoffe:
- Lagerbaustahl SUJ2: Ideal für Messer zum Schneiden von Papier, Karton und anderen Materialien, die keine hohe Festigkeit oder Verschleißfestigkeit erfordern.
- Legierter Werkzeugstahl 9CrSi: Geeignet für Messer zum Schneiden weicher Materialien wie Holz.
- Kohlenstoff-Werkzeugstahl SK5: Bekannt für seine Elastizität, eignet es sich zum Schneiden von Kunststoff, Polyethylen und Weichmetallen.
- Für komplexere Aufgaben:
- Korrosionsbeständige Edelstähle wie SUS420: Perfekt für aggressive Umgebungen und die Lebensmittelproduktion, mit hoher Härte (55 HRC) und Oxidationsbeständigkeit bis +450 °C, wodurch sie ideal für den wiederholten Gebrauch sind.
- Matrizenstahl SKD-11: Bietet hervorragende Verschleißfestigkeit und eignet sich daher für Guillotinemesser unter rauen Bedingungen.
- Schnellarbeitsstahl HSS: Führend in der Verschleißfestigkeit und in der Lage, verschiedene Metalle zu schneiden.
Schlüsselfaktoren bei der Stahlauswahl:
- Härte: Bestimmt Schnittigkeit und Lebensdauer.
- Verschleißfestigkeit: Widerstandsfähigkeit gegen Beschädigung und Verformung während des Gebrauchs.
- Elastizität: Fähigkeit, nach einer Verformung in die ursprüngliche Form zurückzukehren.
Die Wahl des richtigen Stahls ist entscheidend für die Effizienz und Langlebigkeit von Industriemessern.
Anwendungsbereiche
Industriemesser sind in vielen Branchen unverzichtbare Werkzeuge. Ihre Steifigkeit und Festigkeit variieren je nach Aufgabenstellung und ermöglichen so maßgeschneiderte Lösungen für spezifische Aufgaben.
In der Papierindustrie beispielsweise werden Scheibenschneidwerkzeuge häufig für die präzise und effiziente Materialbearbeitung eingesetzt. In der Metallverarbeitung eignen sich Guillotinemesser hervorragend für die Bearbeitung hochfester Materialien.
Zum Trennen von Polymeren oder Stoffen werden gezahnte Messer mit geschärften Metallklingen eingesetzt, die glatte und saubere Schnitte gewährleisten.
Industriemesser werden häufig in Bereichen wie Verpackungsanlagen, Metallschneidemaschinen und industriellen Fleischwölfen eingesetzt und stellen ihre Vielseitigkeit und Zuverlässigkeit in verschiedenen Produktionssektoren unter Beweis.
Merkmale der Messerbedienung
Die beim Materialschneiden eingesetzte Trennübergangstechnologie weist besondere Merkmale auf. Ein wesentlicher Faktor ist das schnelle Eindringen des Schneidwerkzeugs in die Materialstruktur, was zu steigenden Kraftbelastungen führt. Im Gegensatz zu anderen Verfahren gibt es keine stationäre Phase, in der die Belastung konstant bleibt. Nach Erreichen eines Spitzenwerts fällt die Kraft stark ab, begleitet von einem Materialbruch durch Spaltung oder plastische Scherung.
Im letzten Schritt wird der Schnitt durchgeschoben, wobei erneut mehr Kraft aufgewendet werden muss, um die Reibung zu überwinden und Materialreste zu entfernen.
Der Prozess variiert je nach Material. Bei erhitzten Rohlingen, insbesondere aus kohlenstoffreichen Stählen, ist diese Technologie weniger effektiv. In diesem Fall sind alternative Trennverfahren empfehlenswert.
Der Widerstand bei der Materialtrennung ist abhängig von:
- Spezifische Schnitt- oder Scherkraft: Die Kraft, die pro Flächeneinheit zum Trennen des Materials erforderlich ist.
- Schnittgeschwindigkeit: Die Geschwindigkeit, mit der sich das Schneidwerkzeug bewegt.
- Nominale Lücke: Der Abstand zwischen der Schneide und dem Material.
- Materialstärke: Die Menge des zu schneidenden Materials.
- Kunststoffeigenschaften: Relative Penetrations- und Verformungseigenschaften, die das Materialverhalten unter Belastung beeinflussen.
Der Operationsverlauf lässt sich in fünf Phasen unterteilen:
- Elastische Kompression: Die Belastung durch das Schneidwerkzeug übersteigt nicht die Scherfestigkeit des Materials, ohne dass es zu sichtbaren Veränderungen im Querschnitt oder Aussehen kommt.
- Kunststoffdurchdringung: Beginnt, wenn die Schneide die Festigkeitsgrenze des Materials überschreitet, was zu Schichtscherung und Spitzenkräften führt.
- Bruch: Risse bilden sich und breiten sich vom Rand nach innen aus, wobei sie Spannungskonzentrationspunkten und dem Weg des geringsten Widerstands folgen und so die Kraft reduzieren.
- Vollständige Trennung: Der Schnittabschnitt löst sich vollständig, wobei die Kraft aufgrund der Reibung nachlässt.
- Durchsetzen: Eine letzte leichte Kraft entfernt das abgeschnittene Stück.
Bei spröden oder weichen Materialien wie Kunststoff erfolgt die Trennung kontinuierlich ohne Stoßeinwirkung.
Beachten Sie, dass dies eine allgemeine Beschreibung der Trennübergangstechnologie ist. Spezifische Implementierungen können je nach Ausrüstung, Materialtyp und anderen Faktoren variieren.
Messerherstellung Nach Zeichnungen
Industriemesser werden in der Regel nach Kundenzeichnungen oder Skizzen maßgefertigt. Ob für Metallschneid- oder Holzbearbeitungsmaschinen – die Zeichnung gibt alle notwendigen Parameter, Formen und Konfigurationen vor. Manche Kunden bestellen jedoch Messer nach Muster, was im Vergleich zur zeichnungsbasierten Fertigung zu geringerer Präzision führen kann – ein zu berücksichtigender Faktor.